Customer Case Study – Vopak Chemical Logistics
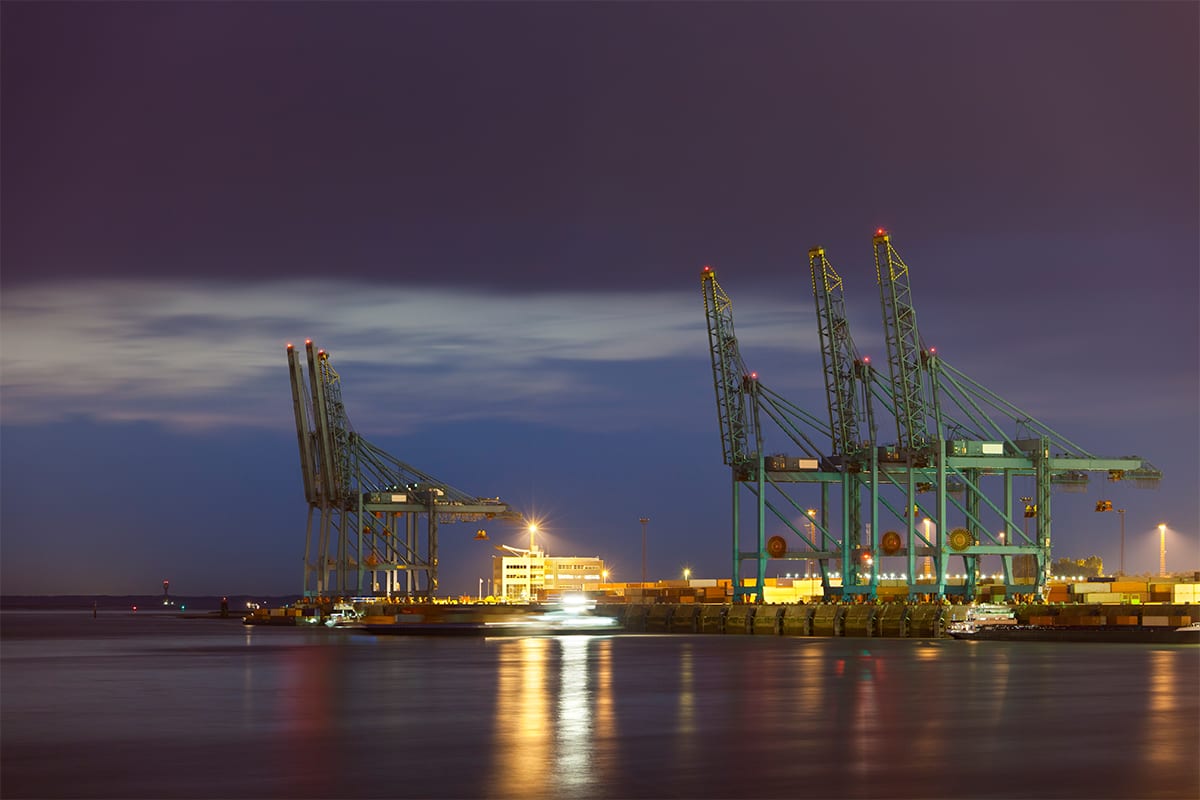
Royal Vopak
Royal Vopak is the world’s largest independent tank terminal operator specializing in the storage and handling of liquid and gaseous chemical and oil products. At the time of the project, Vopak operated in 78 terminals with a storage capacity of more than 26 million cubic meters in 31 countries. The majority of its customers are companies operating in the chemical and oil industries. As part of Royal Vopak, Vopak Chemical Terminals Netherlands (herafter referred to as “Vopak”) is determined to be the most reliable and cost effective partner for chemical producers, consumers, distributors and traders for the storage of handling bulk liquid chemicals and gases in the Benelux region.
The Challenge
More than a 100 trucks per day load and unload the chemicals to or from the 400 tanks at the storage facilities at the three terminals (Botlek, Chemiehaven and TTR) in Rotterdam. To solve the daily puzzle of designating the right slot to each road carrier, reliable data is essential.
The planning process of designating slots is complex and very dynamic. More than two third of the bookings are made only one day in advance. Furthermore, last-minute order changes, multiple order rules, blend orders and various loading and terminal restrictions have to be taken into account.
The communication between the Vopak planning department and the road carriers was done via e-mail, fax and telephone. Vopak was looking for a way to optimize this process. After a thorough selection process Ab Ovo was asked to develop and implement a tailor-made Slot Booking System that had to be deployed in the current ICT architecture.
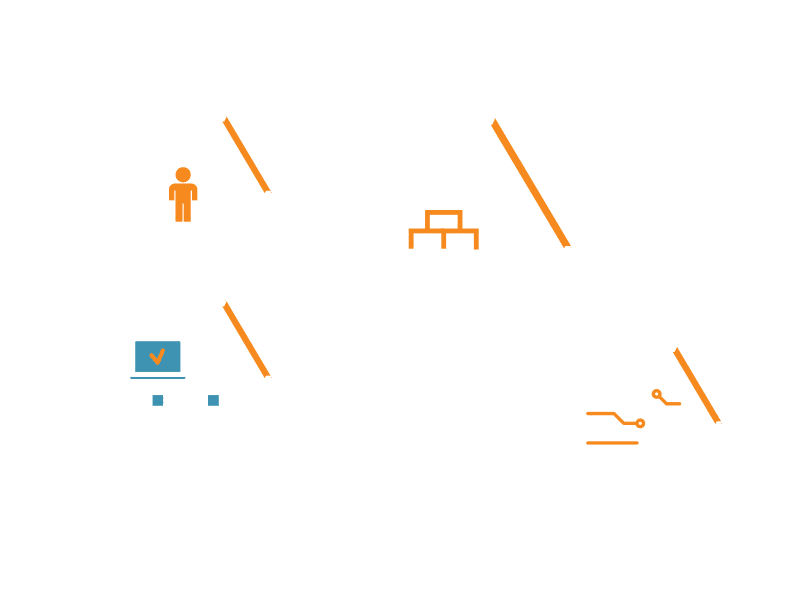
After going live with the system, we received several positive responses of the road carriers we work with. They find the booking of slots much more transparent now.
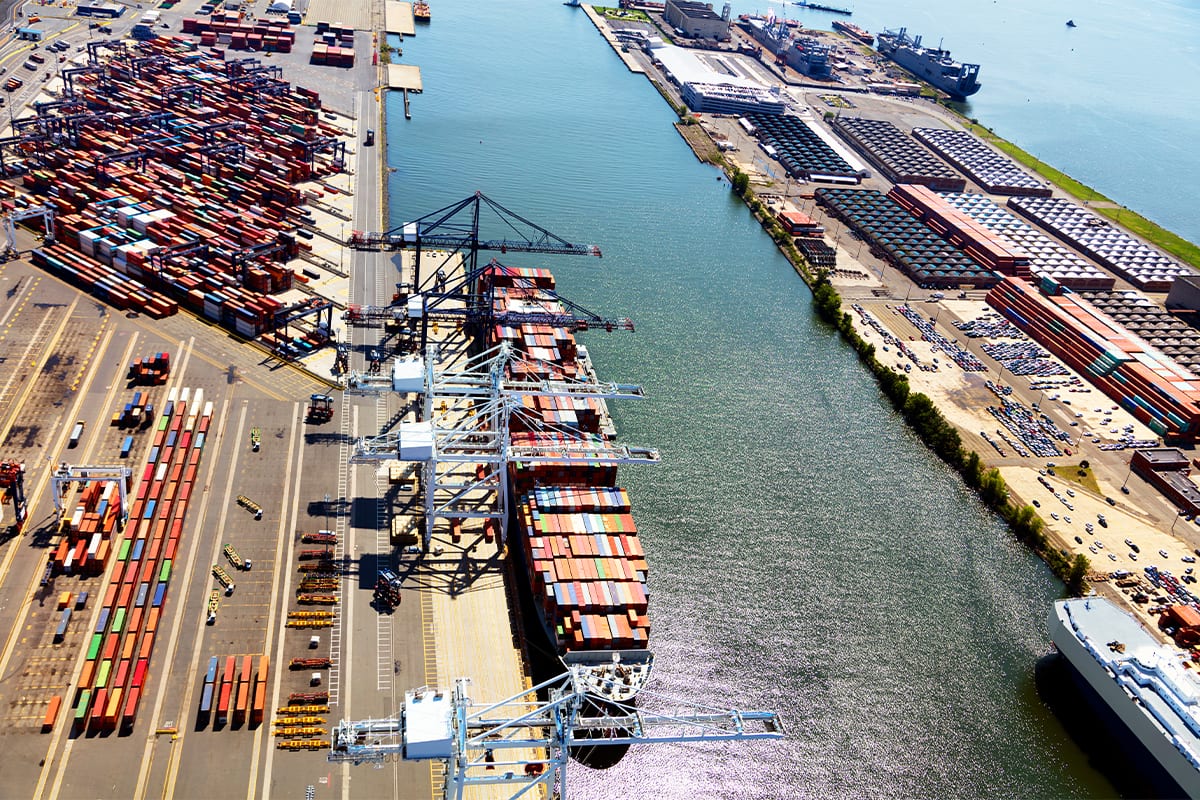
The Solution
Because of the specific business process at Vopak, it became clear that a tailor made solution was required. For the development of the Slot Booking System, Ab Ovo’s in-house Model Driven Architecture development tool TET was used. With TET, tailor-made applications can be realized against substantially lower costs.
The first step was to analyze the desired working methods and procedures of the slot booking process. The planning part of the solution was particulary complex. Variables such as infrastructure constraints and availability (including exclusions), optimization of the use of loading bays and the availability of the rquired number of operators mean a lot of mathematics and optimization programming.
After the analysis phase the business model was specified via interactive modeling sessions with the users. At the same time the test plan and test environment was set up and the architecture advice was presented. After the completion of the business model, the new system was implemented at the three terminals. Besides this, Ab Ovo developed user manuals for all Vopak’s transporters and thoroughly tested the system.
The Result
With the Slot Booking System road carriers are able to book slots directly via a secured personalized webpage at the Vopak terminals Botlek, Chemiehaven and TTR. Logging on is done with and account name issued by Vopak. A booking can be made with data from Vopak and its customers. If there is no slot available, the road carrier contacts the Vopak planning department to find a solution. After the time slot is booked, the slot can also be changed or cancelled.
Around 300 users work with the system in the Netherlands and over the years Vopak has implemented the system in other locations in the world as well. With the Slot Booking System, data is much more transparant and reliable. For the Vopak planners as well as for the road carriers. The Slot Booking System is fully integrated in the current ICT architecture. Interfaces are made from and to the order processing system. The maintenance of the system is carried out by Ab Ovo.
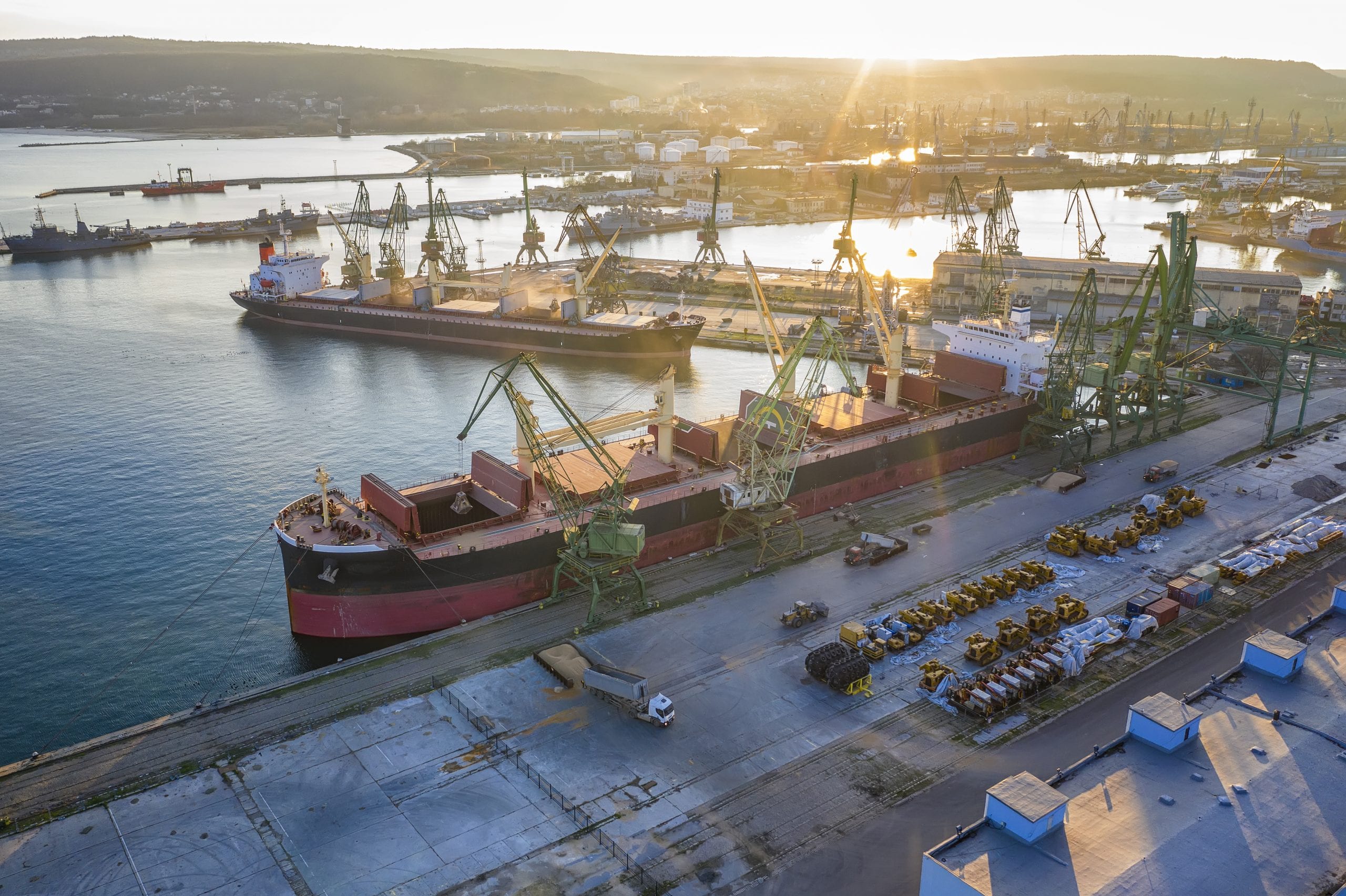
For our planning department the data is much more reliable and all restrictions are automatically taken into account
Landside Logistics – Use Cases
A glimpse into our use cases for landside logistics divided into operational use cases and use cases for advanced analytics.
Operational
- Optimal route & load/unload planning
- Intermodal planning
- Synchromodal planning
#UseCases
Advanced Analytics
Automated damage detection
Camera footage to scan cargo and trucks for damage detection and automatic administration
Data driven contracting
Flexible contracting based on actual data for a better fit with operations
Self learning demand planning
Predict demand based on self learning models that learn directly from the day-to-day situation
Advanced dashboarding
Interactive and advanced dashboarding that allow monitoring of the data ambition
You may find this interesting too
Case Study Hupac
With the ever increasing importance of optimization of resource utilization, we chose the Advanced Planning & Scheduling solution, provided by Ab Ovo, to digitize our intermodal capacity planning.
Whitepaper Synchromodal
Ab Ovo’s Synchromodal Solution processes all needed transport information for optimum planning scenarios, resulting in emission reduction & high cost savings.
Solution Sheet
Ab Ovo transforms your intermodal logistics by providing end-to-end visibility of your entire planning network.