Customer Case Study – KLM Catering Services Schiphol

KCS
KLM Catering Services Schiphol (KCS) prepares and delivers 45,000 meals a day for 5 airlines and 350 flights. The 1,300-person company is a subsidiary of KLM Airlines and is the catering company for KLM and KLM Cityhopper, as well as Kenya Airways, China Airways and Etihad Airways. KCS also manages non-food supplies to the private airport lounges in Schiphol Airport, sales trolleys and navigation bags.
The Business Process
The business process at KLM Catering Services is unique for the following main reasons:
- The goods that the company transports, vary greatly from day to day in number, content, shape and packaging;
- There are extremely strict food hygiene rules (HACCP norms) and product quality regulations, to follow;
- Due to the nature of airport operations, there are always last-minute orders, gate changes, flight schedule revisions and unexpected on-board material deliveries;
- Regulations stipulate only trained personal can perform certain tasks. Production is done in a shift pattern, respecting both legal requirements and company identity requirements.

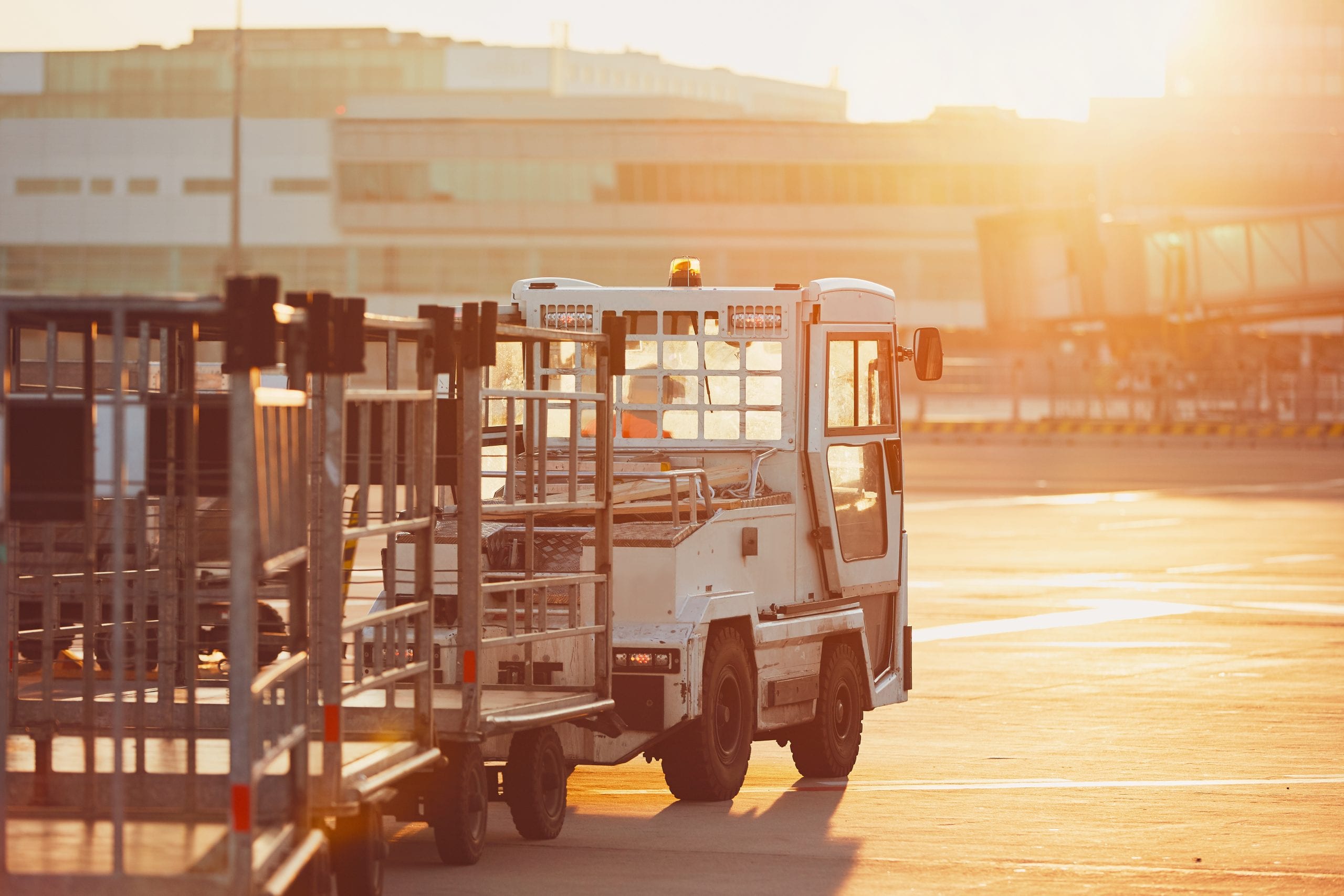
The Challenge
Production of airline meals is demand driven. The demand varies greatly over time, due to seasonal influences, flight schedules, weather or destination of the flight. To absorb the fluctuations in demand, KCS uses a large flexible workforce layer on top of their own staff. Generally speaking, the skill set of direct hires is bigger than the skill set of temporary staff. The planning of this flexible layer is directly controlled by KCS. This allows KCS to determine which temp workers to hire and which skillset is needed. The challenge is to plan the KCS staff as efficient as possible, so the available skills are maximized. The rest of the workforce is hired from temp agencies, preferable for positions that require limited skills.
The Solution
The planning solution provides a complete view of all aspects of the manpower planning puzzle to the planner:
- Demand information for the production floor based on the flight schedule and passenger loads is imported. This results in a workload per workplace (e.g. packaging line, wash bin, tray composition line) per timeframe. For each workplace, the required skills are shown.
- Staff information is imported from the HR system. This includes contract hours, employee roster, default department, planned holidays, and available skills. It also includes default shift pattern information.
All this information is combined in the planning system and the system calculates the optimal distribution of staff over the various workplaces, based on the large set of business rules, like:
- Preferably work on your default workplace, but plan staff on other positions if needed.
- Preferably work in your own shift pattern, but deviation is possible.
- Preferably work within your own department, but department exchange is possible.
- Finally, all vacant positions are filled with temporary staff. The system generates orders for the agencies supplying the staff.
For the long-term planning, the system indicates whether training is needed to increase the skill set of direct hires to better match the required skills. It also offers functions to support the holiday planning process. Solving the holiday puzzle (“Which requests can be approved?” and “if approving a request leads to a shortage, can it be approved if the requests starts a day later?”) is made easier by letting the planner play with the requests by moving the requests around, shorten the duration and extending it.The result is visualble immendiately in an employee availability Gantt chart.

“With eHRM, we make a significant step to improve our operational excellence. The optimal deployment of our entire workforce would not have been possible without this solution. We now plan our skilled workforce as optimal as possible, ensuring our service to our customers”
The Results
With help of the system, the overall hire of temporary staff decreased. Besides the decrease, the overall skill level of temporary staff decreased, meaning cheaper staff is hired. The system also supports the approval process of ad hoc vacation days and pushes this decision to a lower management level in the organization. Finally, the overall administrative burden on the organization in case of shift swaps, ad hoc vacation days, leaving early, sick leave, overtime etc, decreased. This is now managed directly in the system instead of via paper.
Aviation – Use Cases
A glimpse into our use cases for aviation divided into operational use cases and use cases for advanced analytics.
Operational
- Fluctuating Air Cargo and Passenger Demand
- Air Cargo Network Planning
- Planning your Airport Workforce
#UseCases
Advanced Analytics
Aircraft health monitoring
Pattern recognition to predict when airplane /equipment need maintenance on a unit by unit basis
Improved bagage handling
Predict the journey baggage will take to identify possible bottlenecks and act accordingly
Self learning demand planning
Predict demand based on self learning models that learn directly from the day-to-day situation
Advanced dashboarding
Interactive and advanced dashboarding that allow monitoring of the data ambition
Our Aviation Offering
#FeaturedSolutions

Fleet and Network Planning
Operate in a more flexible network, by allowing flight schedule and fleet configurations to deal with rapidly changing circumstances.
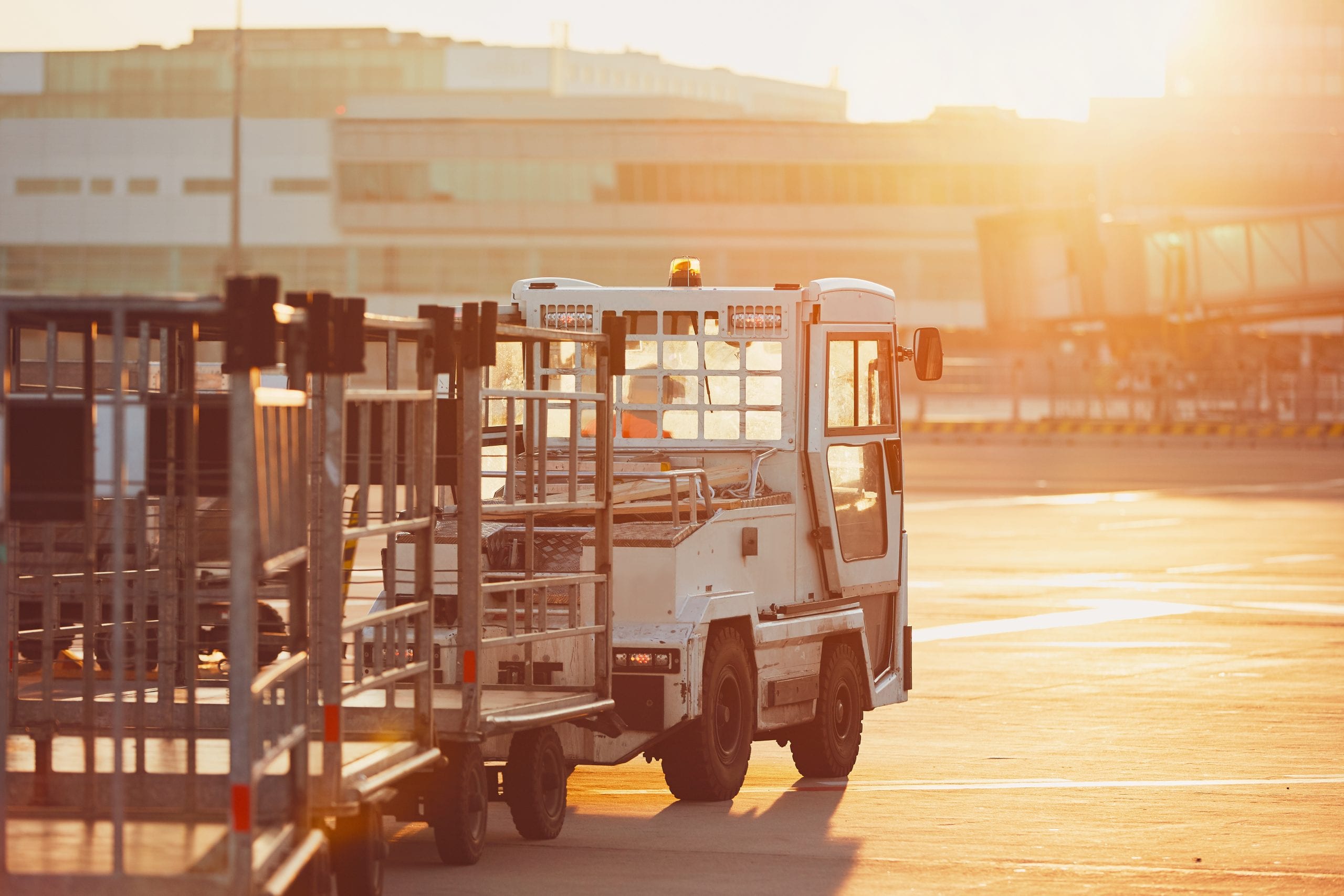
Aviation Ground Handling
An integrated solution for joint planning and scheduling of multiple ground services processes.
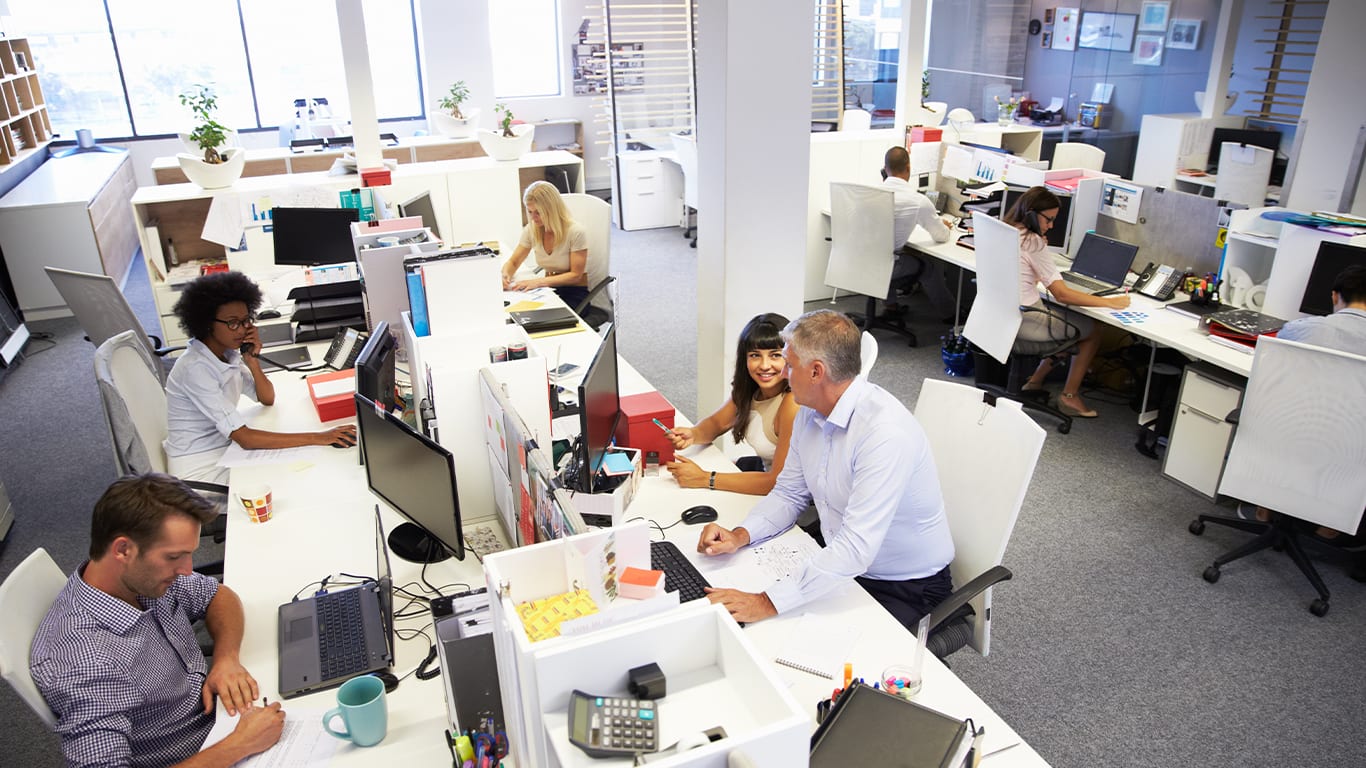
Aviation Workforce Planning
Combine demand and staff information in the planning system and the system calculates the optimal distribution of staff over the various workplaces.