Applications in infrastructure, asset management and internal logistics
Digital twins form digital representations of real world physical entities. They refer to digital replicas of existing or potential future physical assets or processes. While the concept of a digital twin was introduced by Michael Grieves in 2002, underlying technology has in the meantime come to a level to allow for real world and real time digital twin applications. Ultimately building the bridge between the physical and virtual world.
Technology behind digital twins
Digital twins utilize IoT based sensor data, cloud technology, machine learning and advanced analytics to create virtual representations of the physical world. In a first step the physical items are equipped with sensors constantly monitoring different parameters, for instance current position or temperature of the physical item. These sensors are connected to a cloud-based system processing all data these sensors transfer. The data is then analyzed applying advanced analytics to provide immediate feedback, allowing to optimize processes in real-time.
With logistics often being a cost-sensitive business process, the application of digital twins is not as widespread as expected. However, costs for underlying technologies are reducing. Furthermore, many enterprises have already implemented connected technologies such as, sensors, mobile scanners or cloud-based IT systems.
All these developments make digital twins today, a business case worthwhile to explore in logistic applications. In the next paragraph, we dive deeper in three potential application areas of Supply Chain Management: infrastructure, asset management and internal logistics.
Digital twins in Infrastructure
COVID-19 is one more recent example of the importance of resilience in infrastructure systems. Whether looking at the aviation, rail or maritime industry, infrastructure experience uncertainties from short-term shocks. Frequently, these shocks are based on events being unpredictable by nature.
Digital twins enable enterprises to cope with these uncertainties. Based on processed real-time data the digital twin supports what-if scenarios and therefore empowers enterprises to build up more resilient infrastructure systems.
In the UK, the rail transportation company Alstom has developed a digital twin to optimize its maintenance operations. The digital twin includes data from all trains, time tables, real time locations and maintenance depot capacities in order to create a digital representation of the network. Unexpected disruptions are processed in real time and the maintenance plan is adopted. Beside that what-if analysis can be conducted in order to create a more resilient network overall.
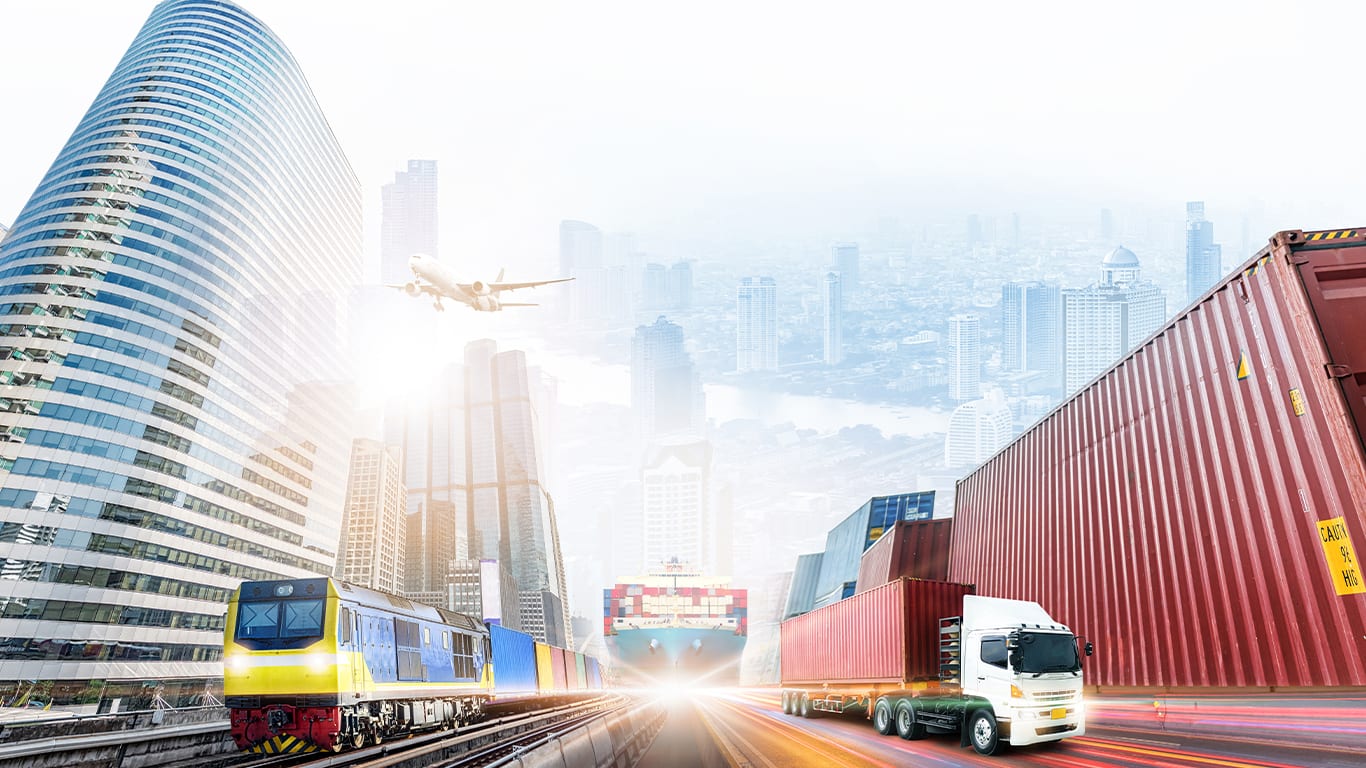
Digital twins for logistic assets
Digital twins can also be used for monitoring and optimizing asset performance. For instance sensors can be equipped to rail wagons, locomotives or also forklifts in distribution centers. These sensors will then transmit data about temperatures, speed, position or shock waves. Data which can be used to optimize performance or to create preventive maintenance plans that are based on the real maintenance demand of each individual asset. By sending alerts for assets at risk of unplanned downtime, potential revenue losses or larger equipment repair costs are avoided.
Applications for digital twins in asset management are widely spread. Deutsche Bahn, for example, sees potential applications for digital twins for around 3,000 signal boxes, 70,000 switches or 5,400 stations with countless display panels, clocks, elevators and escalators.
Digital twins for internal logistics
In terms of internal logistics, digital twins are a powerful tool to build digital replicas of distribution centers, warehouses or shop floors. Here the digital twin can constantly monitor the network interactions of various automation technologies, for instance automated vehicles, product picking systems and automated storage equipment. Analyzing this collective data pool allows to interfere with disruptions in nearly real-time, but also enables enterprises to holistically optimize the warehouse / shop floor layout in the mid- to long-term.
Tetra Pak, for example, implemented a digital twin solution for its warehouse in Singapore and achieved a minimum of 16% efficiency gain due to less congestion, improved resource planning and smarter workload allocation. The solution allows them to constantly monitor material flows, environmental conditions and sends alerts in case of disruptions. Operational risks were reduced leading to an improved employee safety.
Digital twins at Ab Ovo
Ab Ovo, headquartered in Rotterdam, has been delivering advanced analytics in the field of supply chain to their customers for over 20 years. We specialize in business process analytics where our 80+ specialists like operations research experts, mathematicians and business consultants digitize a supply chain process, quantify it and subsequently build prediction models (machine learning) or optimization models on top of it. Our business translators have extensive experience in supply chain process optimization which allow them to act as the linking pin between business and analytics.
For more information, please contact us or check our use cases.